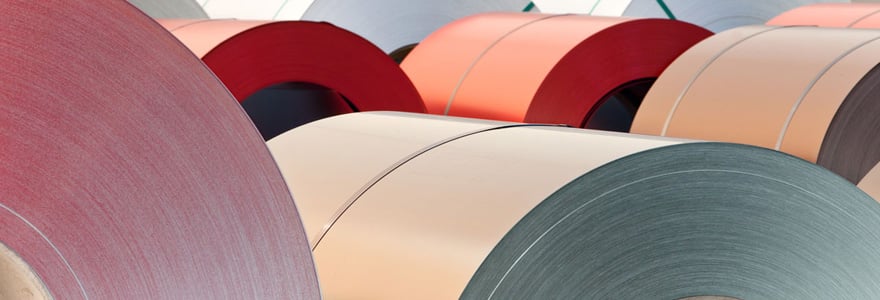
For the past two decades, coil coating has been a critical aspect of the manufacturing industry, especially in the production of radiative equipment. Coil coating involves applying a coating material to a continuous strip of metal, which can then be stamped, formed, or bent into a diverse range of products. The value of coil coating lies in its ability to provide corrosion resistance, enhance durability, and improve the aesthetic appeal of metal products. Additionally, it is an environmentally-friendly, cost-effective, and efficient technique that surpasses traditional painting methods. In this article, we will explore the art and science of coil coating, including the different techniques, advantages over traditional painting, and its applications across various industries such as automotive, construction, furniture, electronics, and radiative equipment. Moreover, we will also examine some of the latest trends in coil coating technology and how they are changing the industry. So, buckle up and join us as we take a deep dive into the fascinating world of coil coating.
The Importance of Coil Coating in the Manufacturing Industry
Coil coating is a highly effective process that involves painting rolls of metal sheets before they are processed into final products. This process is essential in the manufacturing industry due to its numerous benefits in final product quality and longevity. Below are some key reasons why coil coating is a crucial process in turning raw materials into finished products.
Protects Against Corrosion and Wear
One of the significant benefits of coil coating is improved resistance to corrosion and wear. The process of coil coating involves the application of a protective layer that can withstand harsh environmental conditions such as acidic conditions, high humidity, or extreme temperatures. The protective layer prevents the metal sheets from rusting or wearing out, which can affect the overall quality of the final product.
Improves Aesthetic Appeal
The application of paint via coil coating is more advanced than traditional painting methods. This process allows for a consistent and even finish that enhances the aesthetic appeal of the final product. The use of different colors and textures offered by coil coating enables manufacturers to produce products that meet the design preferences and requirements of different clients.
Increases Durability and Longevity of Products
The use of the coil coating process enhances the durability and longevity of the final product by preventing scratches, cracks, or peeling of the painted surface. The process also ensures that the paint does not lose its vibrancy, ensuring that the products maintain their aesthetic appeal for a more extended period.
Coil Coating Techniques
Different techniques are used in coil coating, depending on the requirements of the final product. The three significant techniques used in the industry are: - Roll Coating - Curtain Coating - Electrostatic Coating Roll coating involves the application of paint on metal sheets using rollers. Curtain coating involves a continuous flow of paint falling like a curtain over the sheets to ensure even coverage. Electrostatic coating relies on the attraction between charged paint particles and the metal sheets to ensure maximum paint transfer.
Advantages of Coil Coating over Traditional Painting Methods
Coil coating offers significant advantages over traditional painting methods, such as brush painting and spray painting. The following are some of the advantages: - Consistent and even paint coverage. - Enhanced resistance to corrosion and wear. - Reduced post-processing and cleaning time. - Possibility of using various colors and textures. - Enhanced durability and longevity of products.
Applications of Coil Coating Across Different Industries
Coil coating has a broad range of applications across different industries. Some of the industries that widely use coil coating include:
Building and Construction
The construction industry widely uses coil-coated metal sheets for roofing, wall cladding, gutters, and downspouts due to their enhanced resistance to harsh environmental conditions and long-lasting aesthetic appeal.
Automotive
Coil-coated metal sheets are commonly used in the automotive industry for manufacturing car bodies, chassis, and trims. The application of coil coating enhances the durability and longevity of these parts, making the final product more robust and long-lasting.
Appliances and Electronics
Coil-coated metal sheets are also used in the manufacturing of home appliances such as refrigerators, washing machines, and air conditioners. The use of coil coating enhances the aesthetic appeal and durability of these appliances.
Furniture
Coil coating is a popular application for furniture manufacturing due to its ability to produce a range of finishes, textures, and colors that seamlessly blend in with any interior décor.
Future Trends in Coil Coating Technology
The future of coil coating technology looks promising, with innovation in materials science and engineering essential for improving product quality and reducing the impact on the environment. The latest innovations in this technology include ultra-thin coatings, nanotechnology coatings, and powder coatings that improve product durability, flexibility, and reduce the overall environmental impact. In conclusion, coil coating is an essential process in the manufacturing industry that improves the durability, aesthetic appeal, and resistance to wear and corrosion of final products. The use of different techniques and innovative materials science and engineering ensures that the future of this advanced technology is full of promise.